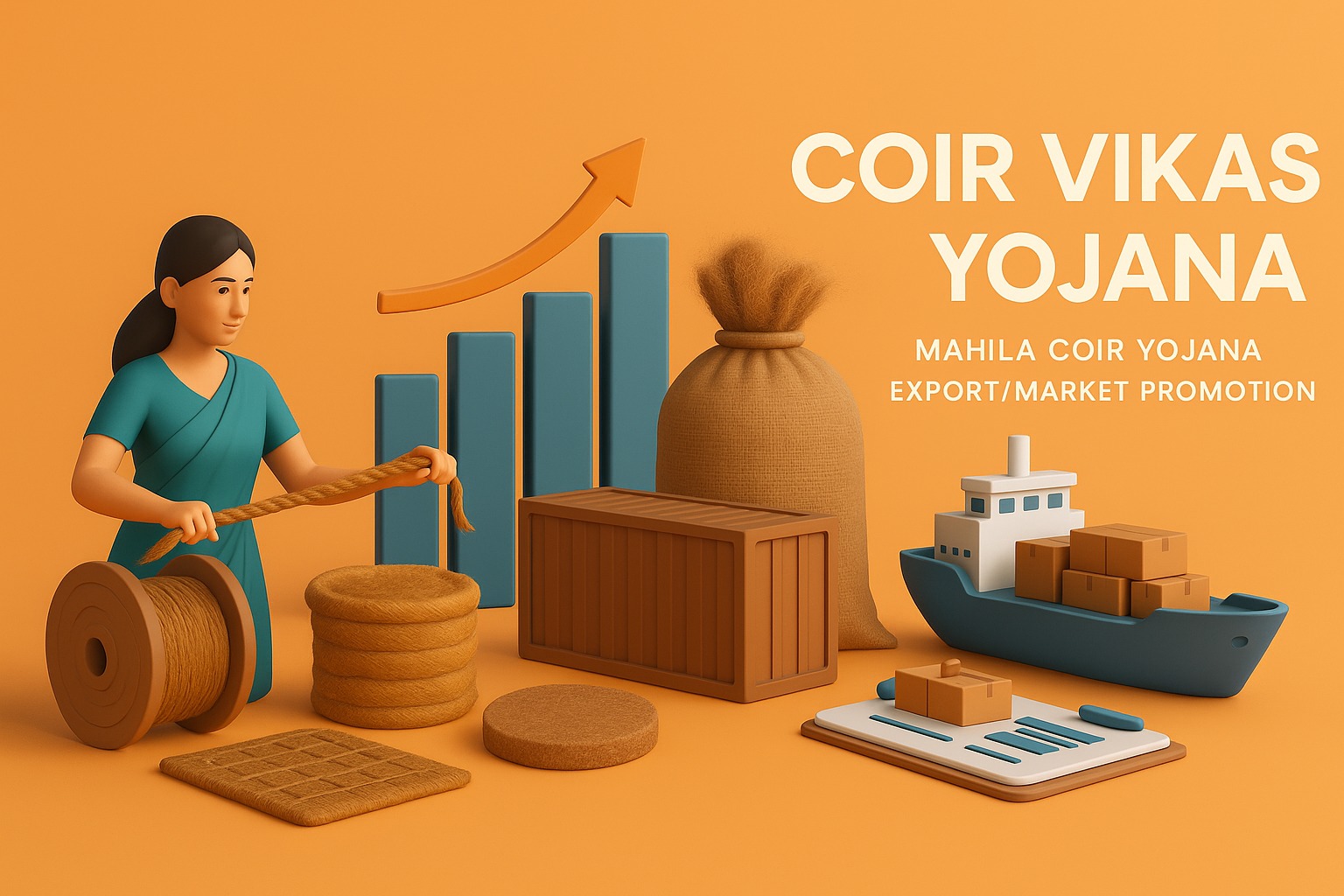
ISO Certification Services by Sigma Solutions
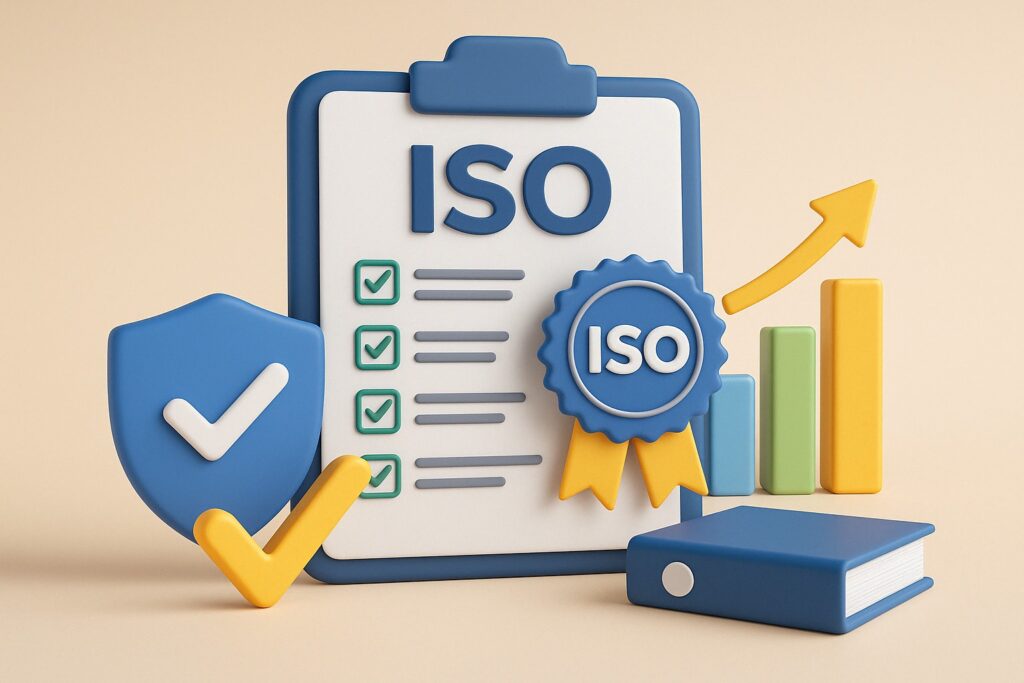
Introduction
In 2024, a medium-sized manufacturing company faced mounting pressure from prospective clients and procurement agencies to demonstrate quality assurance and global standard compliance. Many corporate buyers and government tenders required ISO certification as a minimum qualification to secure contracts.
Despite their operational efficiency, the business struggled to expand due to the absence of recognized certifications such as ISO 9001 (Quality Management System). They approached Sigma Solutions to streamline the certification process, improve credibility, and unlock new market opportunities.
Challenges Faced by the Founders
1. Lack of Awareness About ISO Standards
- The management team was unclear on:
- Which ISO certification to apply for
- The difference between ISO 9001 (Quality), ISO 14001 (Environment), and ISO 27001 (Information Security)
- Whether ISO was mandatory or beneficial for business growth
2. Documentation Complexity
- The company lacked:
- Standard Operating Procedures (SOPs)
- A formal Quality Manual
- Process flow diagrams and structured internal controls
- Team members were unfamiliar with the level of documentation and reporting expected during ISO audits
3. Audit Unreadiness
- No internal system existed for:
- Quality assurance reviews
- Regular audits
- CAPA (Corrective and Preventive Action) tracking
4. Business Disruption Concerns
- Fears that the certification process would:
- Interrupt production and delivery timelines
- Overload teams with documentation tasks and meetings
- Delay ongoing client acquisition and sales
5. Missed Tender Opportunities
- Lost multiple government and private tenders due to lack of certification
- Could not bid for contracts requiring ISO 9001 or ISO 14001 compliance
Solution Provided by Sigma Solutions
Sigma Solutions delivered a comprehensive ISO certification service, handling everything from standard selection to audit coordination and post-certification compliance. The process was tailored to ensure minimum disruption and maximum benefit for the client.
Implementation Strategy
1. ISO Standard Selection & Business Assessment
- Conducted an internal business review to:
- Understand the company’s production processes, quality protocols, and export aspirations
- Recommend ISO 9001:2015 certification as the most relevant starting point
- Provided a 30-day roadmap:
- ISO selection
- Documentation setup
- Audit preparation
- Certification from an accredited body
2. Documentation & Compliance Structuring
- Developed and implemented:
- Standard Operating Procedures (SOPs) for each production line
- Quality Manual customized to their operations
- Organizational flowcharts, risk assessment documents, and control matrices
- Aligned documentation with ISO clause requirements under ISO 9001:2015
- Delivered ready-to-use templates for:
- Quality Objectives
- Internal Audit Reports
- Non-Conformance Reports (NCR)
3. Internal Audit & Staff Training
- Conducted a pre-certification internal audit to identify compliance gaps
- Delivered onsite and virtual training for key departments including:
- Production
- Quality Control
- Sales and Procurement
- Trained staff on:
- Document control
- CAPA systems
- Handling third-party audits with confidence
4. Certification Application & Audit Support
- Helped apply through a globally accredited ISO certification body
- Coordinated the entire audit process, including:
- Scheduling visits
- Liaising with external auditors
- Ensuring smooth audit walkthroughs
- Provided on-call support during audits and real-time gap resolutions
5. Post-Certification Support & Compliance Maintenance
- Advised on:
- Displaying ISO credentials on packaging, website, and proposals
- Preparing for surveillance audits (typically conducted after 6–12 months)
- Set up a compliance calendar for:
- Audit reviews
- QMS updates
- Tender-specific documentation requests
Results Achieved
Outcome | Details |
ISO 9001 Certification | Secured certification within 30 working days |
Business Credibility Boosted | Qualified for government tenders and B2B contracts |
New Market Access | Attracted clients requiring ISO-compliant vendors |
Enhanced Internal Controls | SOPs and quality manuals improved product consistency |
Ongoing Compliance Ready | Set up for surveillance audits and future ISO upgrades (e.g., ISO 14001) |
Conclusion & Key Takeaways
ISO certification is not just a formality—it’s a growth enabler. From improving internal systems to accessing high-value contracts, certification under globally recognized standards gives small and mid-sized businesses a strategic edge.
Sigma Solutions ensured a hassle-free ISO journey by managing documentation, training, audit prep, and certification support. The company now stands out as a certified quality manufacturer ready to compete nationally and globally.
Key Learnings:
- ISO 9001 is essential for manufacturing companies aiming for scalability and market trust
- Documentation is crucial—SOPs and quality manuals lay the foundation
- ISO is not just for compliance—it’s a sales and growth asset
- With expert support from Sigma Solutions, certification becomes a business advantage
Related Services by Sigma Solutions
- GST Registration & Compliance Advisory
- Startup India & Udyam (MSME) Registration
- Trademark & IP Filing for Manufacturers
- FSSAI Licensing for Food Processors
- Business Standardization & Internal Audits
Client Testimonial
“We had no idea where to start with
ISO certification until we contacted Sigma Solutions. They guided us through
every step—documentation, audits, and compliance—making the process smooth and
hassle-free. Thanks to them, we now qualify for high-value contracts and
government tenders.”
— Managing Director, Manufacturing Company – Northeast India